1.1 Redes Industriales
Las redes industriales son aquellas que se encargan de la comunicación digital — intercambio y control de información— entre las distintas partes de un proceso industrial, con la finalidad de mejorar la eficiencia dentro de la fábrica.
Para lograr esto, se debe contar con una estructura de redes moderna, segura y confiable por lo general de fibra óptica, que pueda transportar el flujo de información a los distintos elementos del sistema automatizado, y tener los datos en tiempo real.
¿POR QUÉ ES IMPORTANTE CONTAR CON UNA RED INDUSTRIAL?
Así como en la vida cotidiana las redes de comunicación actual nos mantienen informados sobre cualquier acontecimiento global, de forma similar sucede en el área industrial.
Es importante tener un servicio de comunicación de datos que analice y nos informe de forma automática sobre cualquier situación de los procesos productivos, para poder actuar a tiempo, evitando perdidas o contratiempos.
Además, implementar una red industrial trae más beneficios y es menos costoso que cualquier otro sistema convencional.
VENTAJAS DE LAS REDES INDUSTRIALES
Las siguientes son algunas de las ventajas físicas, funcionales y de ejecución de las redes industriales:
- Mejorar la calidad de los procesos existentes.
- Mejorar la cantidad del flujo de datos.
- Ahorro en el costo de cableado, ya que se optimiza el uso de este.
- Ahorro en los costos de instalación.
- Reducción de los costos de producción.
- Aplicación de sistemas modulares.
- Reducción de cajas terminales y cajas de conexión.
- Facilitar el control de todo el proceso productivo.
- Permitir el uso de dispositivos inteligentes.
- Distribución del monitoreo.
Los sistemas de redes de comunicación industrial se pueden clasificar en diferentes categorías basadas en la funcionalidad:
- Redes a nivel de campo
- Redes a nivel de control
- Redes a nivel de información
Nivel de Campo
Como nivel más bajo, este nivel contiene los dispositivos distribuidos, como sensores (entrada) y actuadores (salida), módulos de E/S y unidades de accionamiento de las máquinas / plantas de una empresa de fabricación que se comunican con los sistemas de automatización a través de un sistema de comunicación en tiempo real.
La transmisión de los datos es cíclica y se caracteriza por un ciclo de bus corto. La duración real del ciclo de bus depende de la aplicación. Varía desde la décima de microsegundo hasta cientos de milisegundos.
Aquí, sólo se transmiten unos pocos bytes al mismo tiempo, por ejemplo, para controlar un actuador o para recibir una señal de un sensor. Sin embargo, al mismo tiempo se producen grandes exigencias en cuanto a la latencia máxima: para poder controlar los procesos de manera correcta, las señales de control deben transmitirse en unos pocos milisegundos.
Profibus DP y Profinet IO cumplen estos criterios y ofrecen las soluciones universales tanto para la automatización de fábricas como para la automatización de procesos.
Nivel de Control
A nivel de planta, los controladores programables (PLC), se comunican entre sí y con los sistemas informáticos de la oficina técnica o de ingeniería utilizando estándares como Ethernet TCP/IP, Intranet e Internet.
Dentro del nivel de control se encuentran todos los sistemas informáticos de automatización (función) que controlan el proceso.
Los controladores están conectados a los sensores/actuadores del nivel de campo y cada uno controla una parte del sistema. Los controladores también están conectados entre sí y con el nivel superior.
En este nivel, la información se transfiere con un tamaño que va de unos pocos bytes a unos pocos kilobytes. La latencia es de una fracción de segundo.
Este flujo de información requiere paquetes de datos y una serie de protocolos de comunicación. Al igual que Profibus, Profinet, basado en Ethernet, ofrece una solución que está siendo bastante utilizada por las empresas para este fin.
Nivel de Información
El nivel de información es el nivel superior de una planta o de un sistema de automatización industrial. El controlador del nivel de planta reúne la información de gestión de los niveles de área y gestiona todo el sistema de automatización mediante el Sistema MES y ERP.
El sistema MES está conectado de forma directa con el nivel de control y los datos de producción actuales. En definitiva, hacen un seguimiento de los detalles de los productos y los pedidos en la planta, recopilan las transacciones para informar a los sistemas financieros y de planificación, y envían de forma electrónica los pedidos y las instrucciones de fabricación al personal de la planta.
Por otro lado, el ERP permite recopilar y organizar los datos empresariales a través de un paquete de software integrado. El software ERP contiene aplicaciones que automatizan funciones empresariales como la producción, la cotización de ventas, la contabilidad, etc.
En este nivel, existen redes a gran escala, por ejemplo, las WAN Ethernet para la planificación de la fábrica y el intercambio de información de gestión. Los datos se transfieren desde unos pocos megabytes hasta gigabytes. La latencia es de varios segundos.
La siguiente imagen muestra un ejemplo de la disposición jerárquica de las redes de comunicación en un sistema de automatización industrial.
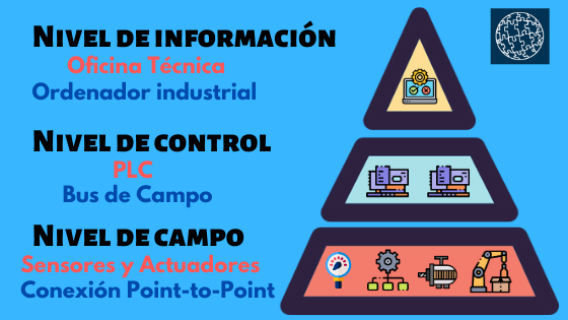
Añadir comentario
Comentarios